Pharmacutical Packaging Gas Control & Testing
- Next-generation optical oxygen analyser for vacuum headspace packaging
- Precision gas mixers that ensure accurate MAP composition
- Industry-leading leak accuracy to 10 microns to reduce unsellable stock
- Reliable packaging testing to prevent reduced potency and compromised appearance.
Gas Control Equipment For Pharmaceutical Packaging
Providing advanced gas control systems for pharmaceutical and vacuum packaging. Our high-performance gas mixers, analysers, leak detection tools, burst testers, and gas flow optimiser enable pharmaceutical manufacturers to maintain accurate and consistent modified atmosphere packaging (MAP) conditions across a wide range of formats.
We also supply oxygen absorbers and desiccants designed to protect product stability by managing in-pack humidity and oxygen levels throughout the supply chain.
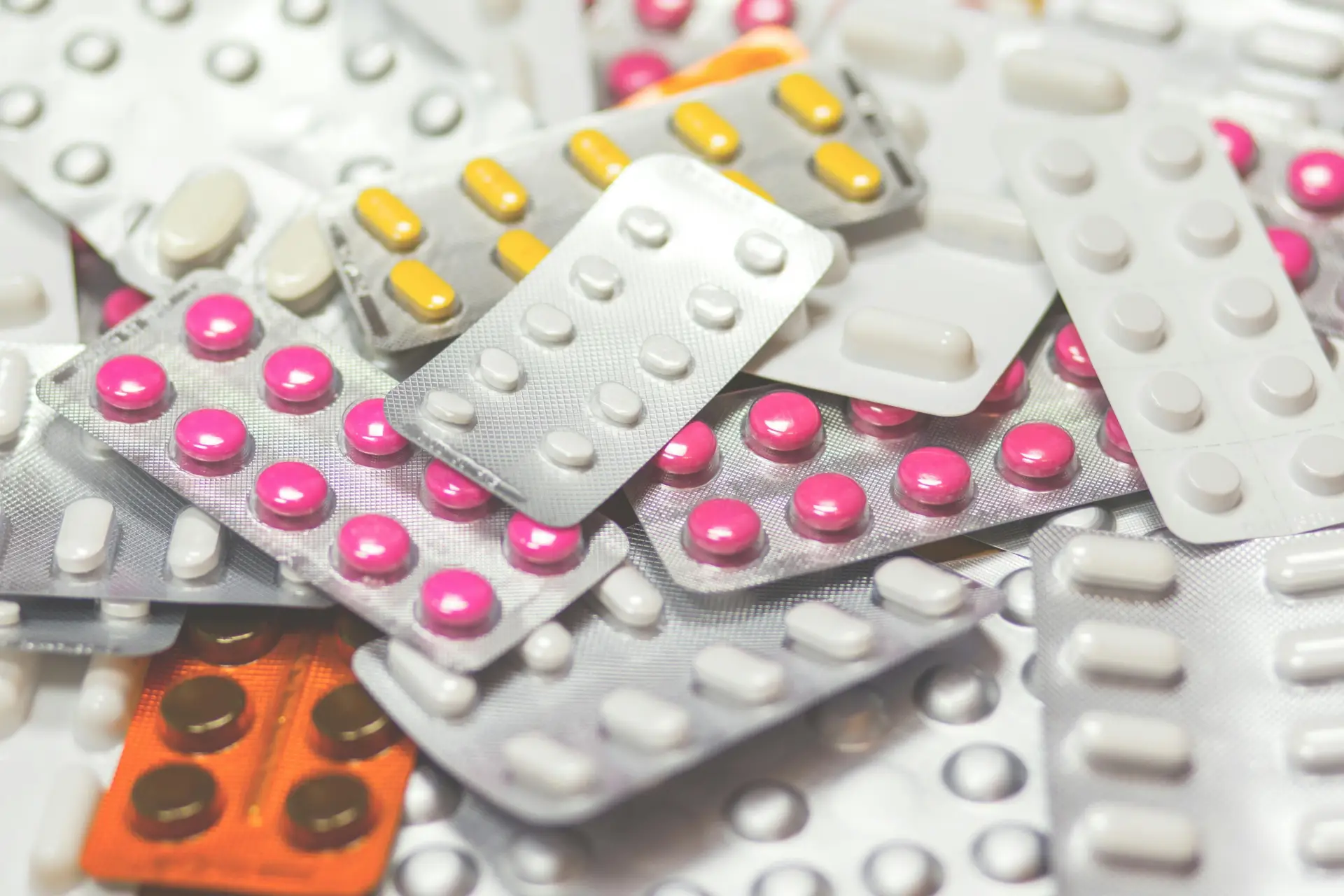
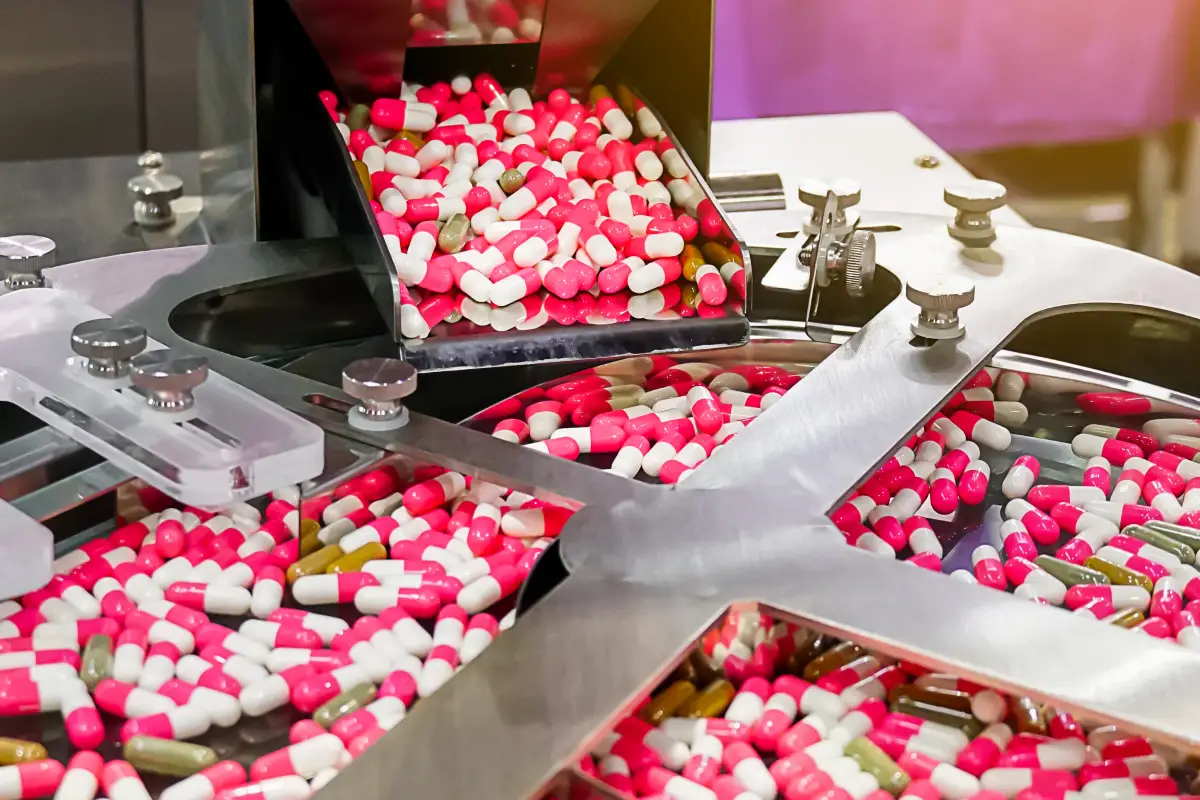
Packaging Quality Assurance For Pharmaceutical Packaging
Pharmaceutical products, including tablets, powders, and injectables, are manufactured, packaged, and distributed globally, often covering long distances before reaching healthcare providers and end users.
Formulations sensitive to moisture or oxygen, such as effervescent tablets and biologics, are particularly vulnerable to degradation during storage and transport.
Even more stable dosage forms, such as coated tablets, are at risk of reduced potency, compromised appearance, or shortened shelf life.
To maintain product integrity and regulatory compliance, pharmaceutical manufacturers use modified atmosphere techniques that limit oxygen exposure, prevent moisture ingress, and support chemical stability.
Accurate gas control is essential for high-value or export-bound products, such as oncology drugs and hormone therapies, where shelf life and quality specifications are strictly controlled.
Gas Control In Pharmaceutical Packaging
The gas composition in medicine packaging depends on the product’s chemical sensitivity, moisture content, dosage form, and shelf life requirements.
Modified atmosphere conditions usually involve minimal residual oxygen and tightly controlled humidity to prevent microbial activity and chemical breakdown.
Excess oxygen or moisture can compromise drug potency, reduce shelf life, or lead to contamination risks, so gas levels must be precisely regulated and monitored.
For oxygen or moisture-sensitive medications, such as powders and effervescent tablets, packaging is often flushed with inert gases like nitrogen to displace oxygen and prevent product degradation.
In sterile injectables, nitrogen is often used to create an inert headspace that protects the medication from oxidation and maintains safety and effectiveness throughout storage.
Active packaging tools, including oxygen absorbers and desiccants, are used to maintain internal conditions. Absorbers reduce oxidation in sealed vials or blister packs, while desiccants protect moisture sensitive products from humidity.
Gas flushing or vacuum/gas cycles are used before sealing to create a stable packaging environment suited to the medication’s stability profile and regulatory standards.
How EMCO Can Help
EMCO is a world leader in testing instruments for modified atmosphere packaging. We support pharmaceutical manufacturers in maintaining product stability and extending shelf life.
Our range of gas control equipment includes semi-automatic desktop systems for precise gas composition testing, seal integrity testing, and burst pressure analysis; accurate gas mixers for modified atmosphere control; and gas flow optimisers designed to reduce gas usage.
We also offer active packaging tools, such as dessicants and oxygen absorbers, to maintain internal packaging conditions and pressurised water baths to detect leaks.
Pharmaceutical manufacturers can use our precision gas mixers to create accurate gas blends and our flow optimiser to control and optimise gas usage during flushing.
For vacuum and low-headspace applications, they can use our state-of-the-art desktop optical gas analyser, which delivers ultra-precise oxygen level measurements in extreme low headspace applications.
Additionally, they can test gas composition, seal integrity, and packaging strength on our semi-automated instruments. They can use our bubble emission testers, constant flow analysis, and bubble emission testers to locate the location of leaks.
Our equipment also captures data that helps optimise the packaging process, improve product consistency, and minimise non-conformity risks.
Why Choose EMCO’s Gas Control Equipment For Pharmaceutical Packaging
- State-of-the-art optical oxygen analyser for vacuum headspace packaging
- Precision gas mixers and gas flow optimisers for optimal MAP conditions
- Semi-automatic (one-tap) sequential gas, leak, and burst testing
- High-accuracy leak detection down to 10 microns
- Quick, easy, and secure testing
- Bubble emission testers to identify leak location
- Test result recording to improve operational efficiency
- Backed by EMCO’s service level guarantee.